Centre for Intelligent Transport
Facilities
On this page:
- Centre for Advanced Robotics at Queen Mary (ARQ)
- Computational Modelling Facilities
- Confocal Laser Scanning and Super-resolution Microscopy Lab
- Electrospray Laboratory
- Flight Simulator
- Hardness Test Machine
- Impact Testing Facilities
- Material Manufacturing Facilities
- Materials Characterisation Lab
- Materials Engineering in Magnetic Fields (MagMat) Facility
- Mechanical Testing Facilities
- Mechanical Workshop
- Nano Fluids Research Labs
- NanoVision Centre
- Photoelectron Spectroscopy Facility
- Polymer Processing Facility
- Q-Arena
- Spectroscopy Facility
- Sustainable Thermal Systems Laboratory
- The Makerspace
- Thermal Analysis Facility
- Thermoelectric Suite
- Undergraduate Teaching Labs
- Whitehead Aeronautical Laboratory
- X-Ray Diffraction Facility
Centre for Advanced Robotics at Queen Mary (ARQ)
The laboratory is equipped with robotic arms, mobile platforms, mechatronic systems and control systems, which are used to research swarm robots, human-like robotic systems, virtual reality interfaces, haptic interfaces, and human motion tracking systems.
Contact: Prof Kaspar Althoefer
Computational Modelling Facilities
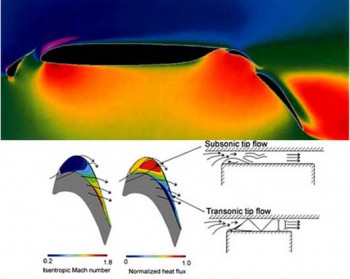
Prediction of flow around : 1- A Multi-Element Wing 2-A Jet Engine Gas Turbine Blade using Computational Aerodynamics.
The Centre has access to the Queen Mary Computing Clusters Apocrita and DERI Andrena, including dedicated use of CPU/GPU nodes for running parallel simulations on-demand. Computational researchers also have access to Tier-1 and Tier-2 national supercomputing facilities, such as ARCHER2, Isambard, CSD3, and Cirrus.
Contact: Prof Sergey Karabasov
Confocal Laser Scanning and Super-resolution Microscopy Lab
A confocal microscopy containing two laser scanning confocal microscopes - a Perkin Elmer spinning disc system and a Leica SP2 with multiphoton laser and lifetime imaging system.
The lab is capable of live cell fluorescence imaging (GFP, calcium imaging etc), 3D reconstruction and morphological measurement, photobleaching assays such as FRAP and FLIP and fluorescence lifetime microscopy(FLIM). The microscopes also interface with sophisticated mechanical loading systems for tissues, individual living cells (micropipette aspiration) and artificial constructs.
Contact: Prof Martin Knight
Electrospray Laboratory
The comprehensive facility enables detailed investigation into the dynamics of droplets and jets using high-speed video cameras, a high-resolution microscope, and a vacuum chamber. Several diagnostic tools are available for measuring the properties of liquids, including a viscometer, a pendant drop tensiometer and an electrical conductivity meter.
Flight Simulator
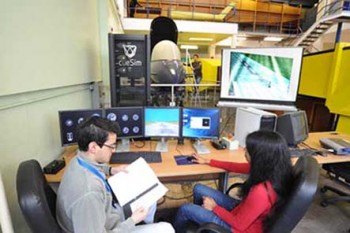
Flight Simulator
The high-fidelity flight simulation training device, which is based on the Airbus A320, is equipped with advanced flight control software, immersive graphics, and an integrated electromechanical system. Its open architecture supports flight simulation research through integration of novel aircraft designs, custom flight control systems, additional airport environments, next-generation guidance and control interfaces, and communication with innovative Air Traffic Management systems.
This facility is currently being upgraded
Hardness Test Machine
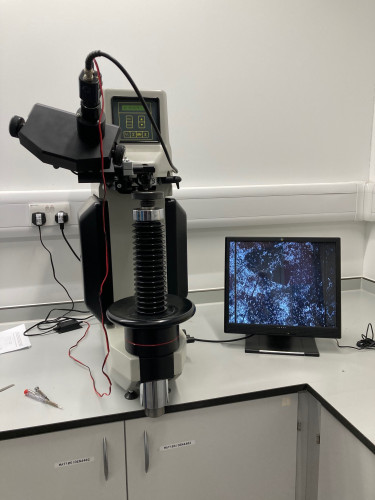
Hardness Test Hardness tester available in G27
Zwick-Roell Hardness Test Machine. Loads from 3kgf to 150kgf. The indenters available are Rockwell diamond and spherical, Brinell (1.0 andf 2.5mm diameter) and Vicker's diamond. At these load levels mainly used for metals and ceramics. There is an attached camera for recording processes.
Contact: Dr Erica di Federico
Impact Testing Facilities
Consists of a gas gun system which can launch objects at high speed alongside a liquid jet impact system to study soft material impact, erosion and penetration. High-quality measurements are conducted using a range of high-speed cameras combined with a split Hopkinson pressure bar for high strain-rate testing of materials.
Material Manufacturing Facilities
The Polymer Processing Facility supports polymer and composites processing, including melt-processing and solution processing. There are also manufacturing suites for fibre-reinforced composite materials and rubbers, alongside capabilities in vacuum-assisted resin-transfer moulding, hot pressing and spark plasma sintering for ceramics.
Materials Characterisation Lab
Contains a variety of analytical equipment to cover a broad range of tests, which are used for structural, thermal and mechanical analysis. The facility offers an analysis service to university-based and external users, both industrial and academic. The lab is located in the Engineering building (Room 232) at the Mile End campus. There are a range of charges for using these facilities.
Contact: Dr Shoghik Hakobyan
Materials Engineering in Magnetic Fields (MagMat) Facility
MagMat is a unique capability in the UK for the synthesis and processing of materials in strong magnetic fields (SMF) known at MagMat. This project provides the initiative for a new era of materials science where magnetic field driven forces are coupled with materials synthesis and processing to produce novel materials. Magneto related phenomena have special relevance to the fields of functional materials and biosciences, where the engineering outcomes are often a result of multifunctional couplings. The use of high magnetic fields in combination with a wide range of processing techniques could lead to new phenomena, materials and manufacturing routes. Our Work is focused on four main research areas of interest where strong magnetic fields can be employed to engineer a wide range of materials - texturing, synthesis, processing and self-assembly.
Contact: Prof Michael Reece
Contact: Dr Salvatore Grasso
Mechanical Testing Facilities
This facility features advanced Instron testing machines for evaluating the mechanical properties of various materials in applications ranging from aerospace components to biomaterials. These systems apply compression, tension, and torsion forces, enabling detailed analysis of materials' strength, modulus, and other key characteristics. The lab can also conduct precise hardness measurements and more complex mechanical evaluations using BOSE systems, including a biaxial tester.
Contact: Dr Erica Di Federico
Mechanical Workshop
The purpose-built, fully equipped mechanical workshop manufactures parts for research projects in the Centre. The workshop contains both manual and CAD/CAM controlled milling and turning machines for high-speed production of complex components using a variety of materials. A state-of-the-art FDM 3D printer enables rapid prototyping in a broad range of thermoplastics
Nano Fluids Research Labs
The School has a rapidly expanding group working on heat transfer from nano-fluids which are liquids containing nano-scale particles that act to alter the fundamental thermo-physical properties of the fluid and so increase heat transfer rates. The specific research includes formulation of nanoparticles and stable nanofluids in a purpose built laboratory. In addition, a new test facility is being constructed to investigate flow and heat transfer behavior of nanofluids in micro-tubes. The research will include mechanistic analysis of micro/nanoscale energy transportation and enhanced heat transfer performance.
NanoVision Centre
The NanoVision Centre is a state-of-the-art microscopy unit which brings together the latest microscope techniques for structural, chemical and mechanical analysis at the nanometer scale (1/1000000 mm). The facility contains an impressive range of electron microscopes, scanning probe microscopes and associated analytical equipment for use in the cutting-edge research being conducted by students and staff.
Contact: Dr Subash Rai, Dr Qasim Zia
Photoelectron Spectroscopy Facility
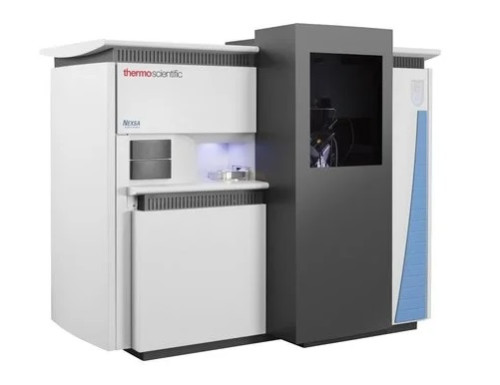
ThermoFisher Nexsa X-ray Photoelectron Spectrometer (XPS) System
A ThermoFisher Nexsa X-ray Photoelectron Spectrometer (XPS) System enables a range of photoelectron spectroscopy measurements on a range of materials. It includes facility for:
- X-ray photoelectron spectroscopy (XPS)
- Ultraviolet photoelectron spectroscopy (UPS)
- Reflection electron energy loss spectroscopy (REELS)
- Ion Scattering Spectroscopy (ISS)
Contact: Dr Richard Whiteley
Polymer Processing Facility
As the first UK Materials department (1967) and one of the five Science Research Council funded Polymer Research Centres in a Materials Department, we have a long standing history and extensive research expertise in polymer and composites processing. Ranging from melt-processing (single and twin-screw extruders, injection moulding, film blowing, solid state stretching) to solution processing (electrospinning, spin coating), a wide range of polymer processing and composites equipment is available at our lab.
Contact: Dr Dimitrios Papageorgiou
Q-Arena
The integrated state-of-the-art research facility enables multidisciplinary, collaborative studies on innovative robotic platforms and control robots, in addition to bi-directional communication between robotic devices and the tracking system. The platform is equipped with six degrees-of-freedom multi-camera tracking, a virtual reality stereo-projection screen and a bimanual haptic interaction system with wearable touch feedback gloves.
Spectroscopy Facility
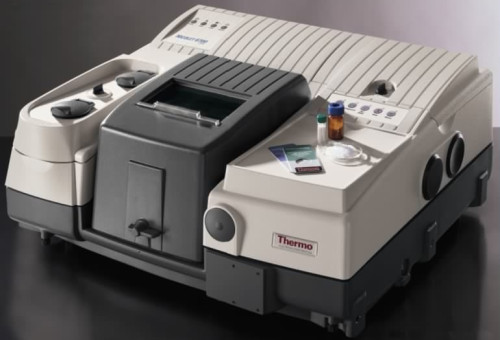
FTIR equipment for materials analysis.
We have a variety of sophisticated spectrometers which are used to identify specific compounds and investigate composition of materials prepared as either a liquid, solid, film or powder. These devices include:
- Fourier Transform Infrared Spectroscopy (FTIR)
- Raman Spectroscopy
- Near InfraRed Spectroscopy (uv-vis NIR).
Contact: Dr Shoghik Hakobyan
Sustainable Thermal Systems Laboratory

Microchannel rig to measure local condensation and flow boiling heat transfer using inverse method.
The School has an international reputation for research into two-phase flow with heat transfer. In particular, it has five test rigs for investigating various aspects of condensation and flow boiling heat transfer which has direct applications to steam power plant, nuclear power plant, organic Rankine cycle (ORC), refrigerators and air conditioners, heat pumps, solar assisted heat pump based heating systems, advanced thermal management of data centre and electric vehicle batteries and air conditioning systems for electric vehicles. These include a microchannel rig for accurate measuring local heat transfer during condensation and flow boiling of low GWP refrigerants and refrigerant mixtures up to high pressure and high temperature and a full tube bank rig for investigating the complex interactions between tube geometry and vapour and liquid flow in real condensers. Several rigs are being used to investigate and optimise highly enhanced finned tubes for increasing heat transfer rates for both internal and external flows and so reducing condenser size. In addition, two calibration baths allow calibration of thermocouples with an accuracy of +/-0.05 K from -15 oC to 200 oC.
Contact: Professor Huasheng Wang
The Makerspace
The Makerspace is an open access workshop for all SEMS and EECS students and staff. It is a space where students can make things, this might be prototyping, model making or simply working on personal projects. The primary aim of the Makerspace is to give students the practical, and creative skills they will require to be effective engineers.
Contact: Mr James Wayland
Thermal Analysis Facility
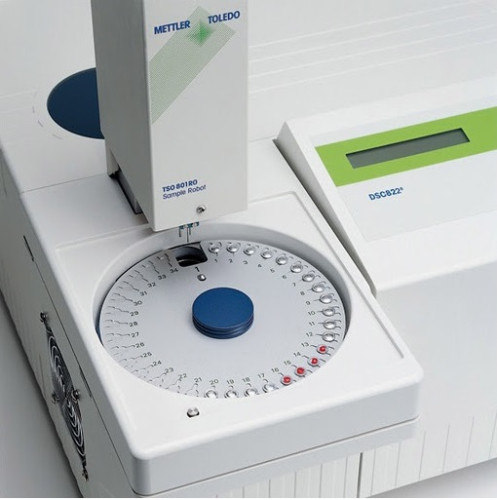
Differential Scanning Calorimeter.
We have a variety of excellent techniques for analysis the thermal properties of materials such as melting temperature, glass transition temperature, viscosity, thermal expansion and thermo-mechanical properties over a range of temperatures (-150 to 1600C). The techniques include:
- Differential Scanning Calorimetry (DSC)
- Rheometery
- Thermo Gravimetric Analysis (TGA)
- Simultaneous Thermal Analysis (STA)
- Dynamic Mechanical Analysis (DMA)
- Dilatometry.
Contact: Dr Shoghik Hakobyan
Thermoelectric Suite
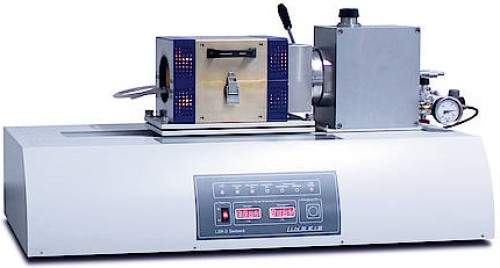
Electrical conductivity and Seebeck measurement (Linseis LSR3)
We house a suite of instruments for the accurate measurement of thermoelectric materials in bulk or thin film form, including:
- Laser Flash Analyzer (Netzsch 453 LFA)
- Electrical conductivity and Seebeck measurement (Linseis LSR3)
- Thin film zT (electrical and thermal conductivity, and Seebeck measurement) (Linseis TFA)
- MMR Seebeck System (MMR Inc)
- Optical in-plane thermal conductivity rig.
- Home-built Seebeck measurement rig.
We also have a bespoke thermoelectric generator testing rig with clamped and air-cooled modes.
Contact:
Prof Michael Reece
Dr Oliver Fenwick
Undergraduate Teaching Labs
We have recently invested £30M in major new teaching laboratories to provide state-of-the-art experimental facilities specifically for teaching.
Opened in 2016 the lab provides a space on the ground floor with step free access and has a height adjustable bench installed for wheelchair users.
Contact: Babatunde Aramide
Whitehead Aeronautical Laboratory
The experimental aerodynamics laboratory contains three low-speed wind tunnels, three high-speed wind tunnels and an acoustics facility. The available diagnostics combine traditional methods (force balances, pressure sensors, flow and surface visualisation systems, hot-wire anemometry) with state-of-the-art optical systems (particle image velocimetry, high-speed schlieren imaging) and microphone arrays to provide detailed flow field information.
X-Ray Diffraction Facility
The X-Ray Diffraction Facility (XDF) offers a full diffraction analysis service in materials science, structural chemistry, structural biology and solid state science. The facility recently welcomed a new Xenocs Nano-inXider SAXS/WAXD system for X-ray scattering, allowing us to characterise advanced materials to a new level of detail.
Contact: Dr Richard Whiteley