Dr Wei Tan
BEng, PhD, FHEA, MIMMM
Research Overview
Mechanics of Materials, Polymer Composites, Modelling and Simulation, Machine Learning, Impact Engineering, Multifunctional Composites, Systems Engineering, Topology Optimisation
Mechanics of Composite Materials Group (MCM Group)
Mechanics of Composite Materials Group (MCM Group) at Queen Mary University London is a vibrant team led by Dr. Wei Tan. Our group focuses on the understanding, predicting and optimising the mechanical properties of composite materials. Lightweight composite materials are finding increasing applications in aerospace, automotive and energy sectors due to their high specific strength, modulus and energy absorption. Particularly, lightweight composite materials that make future vehicles and wind turbine blade lighter and damage-tolerant are particularly relevant to UK in achieving the 2040 net-zero target. The synergy of multi-phase materials often results in unique behaviour of composite materials, outperforming the single-phase constituents. We aim to reveal the deformation and failure mechanisms of composite materials by a combination of experimental, analytical and numerical approaches. This will not only address some fundamental scientific questions, but also accelerate the discovery and development of composite materials.
My research concerns at the understanding, predicting and optimising the mechanical response of composite materials. Particularly, these research projects include:
- proposing novel characterisation methods to reveal the microstructures and deformation/failure mechanisms of composites operating over different length scales;
- developing novel, robust and efficient models for the mechanical response of composites under impact, crush or other extreme loading;
- Intergrate data-driven approaches with advanced computational models to optimise the structural designs.
- promoting a new generation of damage tolerant and multifunctional composites using carbon nanotube materials.
1. Mechanics of Composite Materials: plasticity, fracture, fatigue modelling of composite materials.
Composite structures are susceptible to impact damage, which requires costly and highly inefficient experimental testing to meet safety-critical certification. My project aimed to develop a predictive material model for capturing impact damage and energy absorption capacity of CFRP.
- A multiscale model was also proposed to take into account the physical mechanisms of deformation at different length scales of composite structures. This efficient strategy enables carrying out multiscale modelling from the properties of the constituents (fibre, matrix and interfaces) and homogenise the results into a constitutive model, followed by the transfer of information to the next length scale, which is both time-saving and economical for industry.
- A physically-based model based on crystal plasticity has been proposed to accurately capture the inelastic behaviour and strain rate effect of composites subjected to shear or compressive or impact loading.
- A high-fidelity three-dimensional composite damage model, to predict both low-velocity impact damage and CAI strength of composite laminates, has been developed and implemented as a user material subroutine in the commercial finite element package, ABAQUS/Explicit.
- A crushing model based on a new distorted element deletion strategy was presented to capture the crushing behaviour of composite materials. This model solves the convergence issue due to element distortion under large deformation via deleting element based on the determinant of deformation gradient.
References:
[1] Tan, Wei, and Emilio Martínez-Pañeda. "Phase field predictions of microscopic fracture and R-curve behaviour of fibre-reinforced composites." Composites Science and Techonology (2020). (https://doi.org/10.1016/j.compscitech.2020.108539)
[2] Au-Yeung K, Quintanas-Corominas A, Martínez-Pañeda E and Tan W (2023). Hygroscopic phase field fracture modelling of composite materials.Engineering With Computers, Springer (10.1007/s00366-023-01820-z)
2. Multifunctional composites for energy storage, shape-morphing and sensing
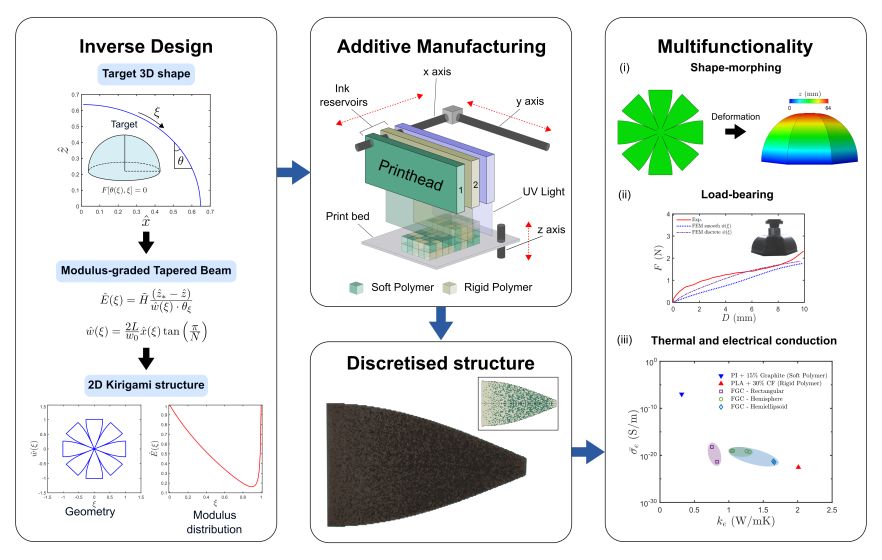
References:
[1] Kansara, H., Liu, M., He, Y. and Tan, W., 2023. Inverse design and additive manufacturing of shape-morphing structures based on functionally graded composites. Journal of the Mechanics and Physics of Solids, 180, p.105382.
[2] Mao JJ, Wang S, Tan W and Liu M (2022). Modular multistable metamaterials with reprogrammable mechanical properties.ElsevierEngineering Structures vol. 272, DOI10.1016/j.engstruct.2022.114976
3. Integrate data-driven approaches with advanced computational models to optimise structural designs.
The adoption of cellular structures for applications involving crash energy absorption are increasing due to their beneficial mechanical properties including low weight and high specific energy absorption. This project aims to integrate the data-driven approach and finite element modelling for designing energy-absorbing composite materials.
References:
[1] Khosroshahi Siamak, Hirak, K., Miguel, B. and Tan, W. Data-driven framework for topology optimisation of energy absorbers. in European Solid Mechanics Conference 2022 (2022).
[2] Kansara, H. et al. Data-driven modelling of scalable spinodoid structures for energy absorption. in UK Association for Computational Mechanics (UKACM) conference 2021 (2021).
4. promoting a new generation of damage tolerant and multifunctional composites for energy storage
Novel direct-spun carbon nanotube polyaniline composite electrodes are developed for supercapacitor applications. Supercapacitors combine high specific power with cyclic stability. Consequently, they find application in regenerative braking systems and in other applications that require high power, short-term energy storage. The influence of charge and discharge rate, electrode composition and state of charge upon the mechanical and electrochemical properties of these novel electrode composites is currently unclear, as are the mechanisms of degradation upon cycling and pre-charging. These topics are addressed in our study.
References:
[1] Koliolios, E., Mills, D. G., Busfield, J. J., and Tan W*. (2021). The Nail Penetration Behaviour of Carbon Nanotube Composite Electrodes for Energy Storage. Frontiers in Materials, 429. https://doi.org/10.3389/fmats.2021.741541.
[2] Tan W, Stallard JC, Jo C, De Volder MFL and Fleck NA (2021). “The mechanical and electrochemical properties of polyaniline-coated carbon nanotube mat.” Journal of Energy Storage vol. 41, DOI10.1016/j.est.2021.102757